Come tradurre ed esaltare l’eccellenza manifatturiera italiana nel nuovo linguaggio della digitalizzazione? Quali sono gli scenari entro cui si sta realizzando la “quarta rivoluzione industriale? Come sfruttare i nostri punti di forza, e cosa possiamo imparare dall’esperienza di chi sta già ripensando il proprio modo di fare industria in ottica digitale? Domande a cui hanno provato a rispondere i tanti relatori internazionali e le figure provenienti dal mondo italiano dell’impresa, della ricerca e delle istituzioni che hanno partecipato a “IoE Talks – La Fabbrica in Digitale”, evento organizzato da Cisco in collaborazione con Intel come convegno inaugurale dell’edizione 2016 di Sps Ipc Drives Italia, in programma alla Fiera di Parma dal 24 al 26 maggio.
Digitaliani e trasformazione
Padrone di casa e grande cerimoniere dell’evento è stato Agostino Santoni, Amministratore Delegato di Cisco Italia. “Fra meno di quattro anni ci saranno 50 miliardi di oggetti e persone connesse alla rete, rispetto ai 15 miliardi attuali e ai 500 miliardi previsti nel 2030. Questo processo di trasformazione ubiquo è la nuova rivoluzione industriale. Come accelerarlo? Combinando la ‘centricità’ delle persone con quella delle cose intelligenti. Entro il 2018 l’interazione macchina-macchina e macchina-uomo sarà riconoscibile. Si può passare dall’automazione industriale a una vera digitalizzazione dei processi riducendo i costi, aumentando i ricavi e diminuendo i rischi. Come? Utilizzando protocolli standard, quelli che hanno reso Internet uno strumento democratico. Con la digitalizzazione si può pensare a un nuovo modo di fare fabbrica. L’impianto industriale a cui puntiamo è connesso e collaborativo in tutte le sue componenti produttive, dalle macchine agli addetti. La conoscenza del contesto è il presupposto per monetizzare le informazioni relative ai prodotti, ai partner e ai clienti e per sviluppare nuovi modelli di offerta a consumo”.
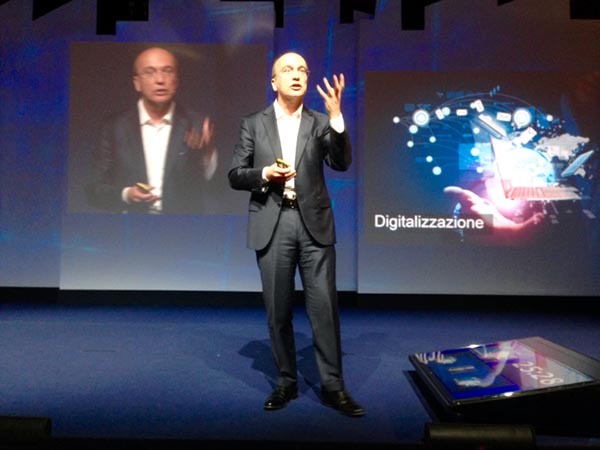
Agostino Santoni, amministratore delegato Cisco Italia
Digitaliani e innovazione
Leda Bologni, Responsabile unità ricerca industriale - ASTER e Membro dell’Organismo di Coordinamento e Gestione di Cluster Fabbrica Intelligente, ha affrontato il tema della rivoluzione digitale evidenziando da subito il ruolo della componente tecnologica ma soprattutto quello delle persone. “Il concetto di persona come infrastruttura si applica perfettamente nelle realtà delle imprese italiane che utilizzano le tecnologie legate al mondo dell’Ict, e quindi reti, high performance computing, IoT e data intelligence, e quelle relative alla produzione come il 3D/4D printing, la fotonica e le nanotecnologie. Tutte queste tecnologie sono utili solo se risolvono problemi e offrono soluzioni. Come? Permettendo di personalizzare i prodotti e adattarli alle specifiche dei singoli clienti, semplificare il lavoro degli addetti e ridurre l’impatto sull’ambiente. L’adozione delle tecnologie richiede nuove competenze e determina nuove prospettive di lavoro”.
“La persona al centro del prodotto”, spiega ancora Bologni, “è la re-configurabilità in tempi brevi, la flessibilità operativa, il software per acquisire i requisiti del cliente, le reti dinamiche, le supply chain integrate e nuovi modelli di business. Cambia il concetto di possesso perché si paga per utilizzare il prodotto in forma di servizio e non per possederlo, e questo cambio di paradigma impatta sulle modalità di sviluppo/progettazione del prodotto stesso. La persona al centro del lavoro comporta invece un salto in avanti nell’interazione uomo-macchina grazie ad interfacce di nuova generazione, nella sicurezza degli ambienti di lavoro, e quindi la loro accessibilità ed ergonomia, e nelle tecnologie per la condivisione dalla conoscenza. I robot non sono una minaccia ma diventano soggetti attivi del processo di produzione: la macchina parla con le persone in modo visuale e non più tramite sistemi a controllo numerico. I tutorial digitali sostituiscono i manuali di istruzione. La persona al centro degli skills, infine, comporta nuovi paradigmi dell’apprendimento”.
Carmine Stragapede, Direttore Generale Intel Italia, ha inquadrato l’argomento della fabbrica digitale confermando una tendenza in atto: “Oggi stiamo andando verso una nuova dimensione industriale perché i costi più ridotti dei sensori li rende più accessibili, i dispositivi sono connessi, i dati continuano a crescere a ritmo esponenziale e con essi l’analisi delle informazioni. Si va verso una nuova fase industriale perché il digitale ha rivoluzionato modelli di business e processi: la capacità di calcolare è diventato un fattore disruptive per le strategie aziendali e l’Internet delle cose è il paradigma della trasformazione digitale. L’IoT è la capacità di mettere intelligenza a qualsiasi oggetto periferico che può generare informazioni da trasferire in cloud e da processare in data center di nuova generazione. L’opportunità dell’IoT per il manifatturiero non è pensare alla fabbrica 4.0 come espressione digitale di vecchi processi ma di portare in fabbrica piattaforme abilitanti, aperte e conformi agli standard, per implementare rapidamente intelligenza, scalabilità, gestione centralizzata e grande disponibilità per la raccolta e l’analisi delle informazioni”.
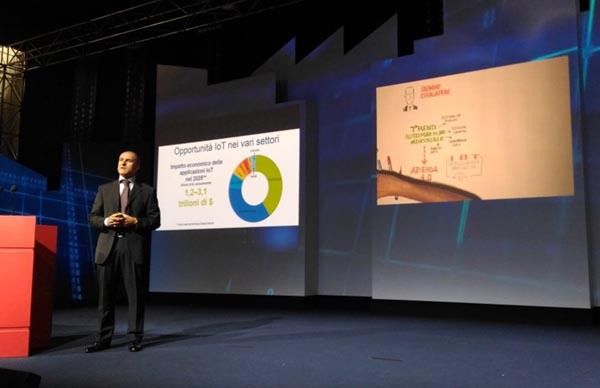
Carmine Stragapede, direttore generale Intel Italia
La seconda parte di IoE Talks ha quindi visto l’intervento di alcune aziende italiane che hanno già intrapreso un percorso di digitalizzazione. Guido Bernardinelli, amministratore delegato de La Marzocco, storico marchio italiano nel campo delle macchine per caffè, ha spiegato che “il grande problema delle piccole e medie aziende è quello di scrivere e costruire una road map e di capire in tempi ragionevolmente certi come utilizzare la tecnologia già disponibile, e da questa trarne vantaggio. La nostra esperienza ci dice che vanno scaricate a terra le potenzialità del digitale dentro una fabbrica artigianale, qual è La Marzocco, che produce soluzioni per un mercato globale. Il digitale è quindi l’abilitatore di nuove opportunità di fare impresa a vari livelli, dalla collaborazione fra addetti e sedi alla connettività del prodotto per controllarne da remoto il funzionamento attraverso un sensore digitale per arrivare alla visibilità di tutti gli asset fisici e renderne più efficiente la gestione. E Cisco ci sta accompagnando in questo percorso”.
Marco Campi, corporate chief information officer di Marcegaglia ha invece sottolineato come la scelta di Cisco nasca dal fatto che “in azienda ragioniamo in termini di total cost of ownership, di gestibilità dell’infrastruttura tecnologica che ci siamo messi in casa e di una road map di sviluppo di soluzioni che ci assicurano la crescita. Siamo un gruppo manifatturiero con 15 fabbriche tutte gestite con un sistema informativo e diversamente automatizzate con sistemi di controllo di processo. Parliamo di connected factory perché c’è un network segmentato di reti Vlan e un’infrastruttura unificata di rete wireless integrata con la rete aziendale e di una security factory perché la protezione di apparati e dati è un asset fondamentale”.
Oronzo Lucia, Automation & Control manager di Fameccanica Group, una realtà di riferimento a livello mondiale nel campo delle macchine per la produzione di prodotti igienici (pannolini e simili) ha offerto una chiara lettura di cosa significhi il concetto di fabbrica digitale per una media azienda. “Le scelte di innovazione dell’azienda vanno sicuramente nella direzione di macchine intelligenti e connesse perché crediamo che l’industrial IoT possa veramente cambiare in meglio il modo di produrre, migliorando il processo di sviluppo e il time to market e di offrire servizi a valore aggiunto. La gestione dei dati è un elemento differenziante della fabbrica intelligente, e sono sia parametri di processo sia informazioni legate ai prodotti: il tutto grazie alla sensoristica, ai sistemi di diagnostica in tempo reale, alle applicazioni di realtà aumentata e ai tutorial digitali per descrivere il funzionamento delle macchine, all’accesso alle informazioni in cloud, alla possibilità di gestire la manutenzione predittiva delle macchine da una console centralizzata. Per arrivare alla massima efficienza degli impianti produttivi”.
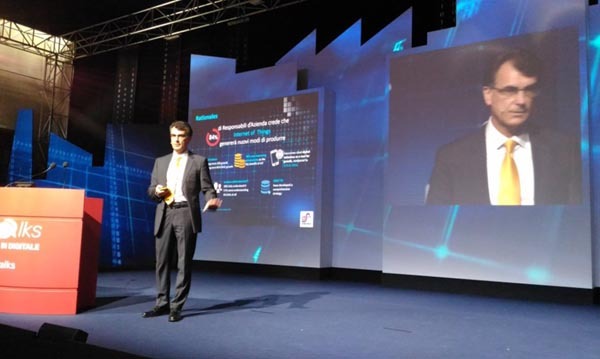
Oronzo Lucia, Automation & Control manager di Fameccanica
Francesco Ciuccarelli, chief information officer di Inpeco, azienda specializzata nel settore dei sistemi per l’automazione dei laboratori di analisi clinica, ha infine illustrato alla platea di IoE Talks come per raggiungere l’obiettivo di rendere più affidabile e sicuro il processo diagnostico “serve conoscere in ogni momento lo stato del campione e garantire sia la sicurezza del processo che quello dell’impianto. L’efficienza si genera con la manutenzione predittiva perché così facendo si assicura la continuità di esercizio delle macchine di laboratorio. La difficoltà sta nell’adattare l’automazione del processo rispetto alle variabili non controllabili. La tecnologia e il digitale sono anche un fattore di attrattività per i nuovi talenti e i millennials. Digitalizzare la fabbrica significa ottimizzare la supply chain, creando – e in Inpeco l’abbiamo fatto con Cisco – l’infrastruttura abilitante per pensare a un’azienda paper less e in cui i servizi arrivano nel cuore della produzione. L’intelligenza degli oggetti e dei componenti è il mezzo per avere un flusso di processo più efficiente, monetizzare i Big Data del processo diagnostico è uno dei pilastri del modello di business”.